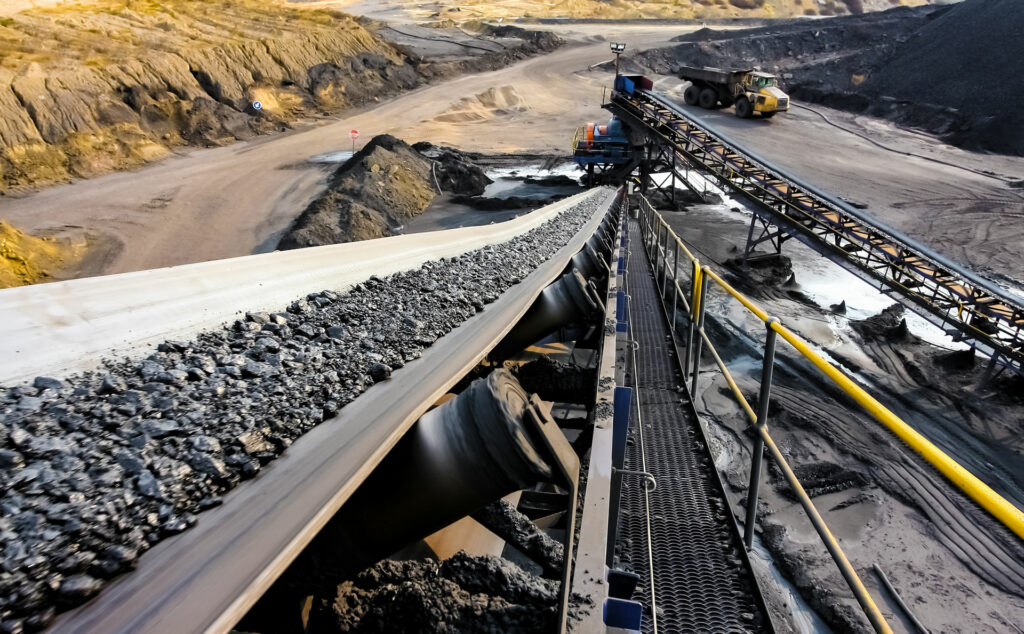
Responsável pela produção anual de cerca de 30 milhões de toneladas de minério de ferro, uma das unidades da principal mineradora de ferro do Brasil, localizada a cerca de 100 km de Belo Horizonte, na cidade mineira de São Gonçalo do Rio Abaixo, conta com três plantas de britagem. Uma delas, a chamada planta de finos, responde por entre 15 a 20% dos minérios processados no complexo.
Resistência e produtividade são essenciais para a produção das mineradoras. Isso porque sua primeira etapa de britagem recebe pedras com granulometria de até 300 mm – matacos – que precisam ser fragmentadas até atingir a granulometria desejada.
Para isso, o minério é levado a um britador de mandíbulas que faz a primeira fragmentação, e o trabalho deste equipamento é crucial para a operação, pois o restante da linha está preparada para trabalhar com granulometrias menores.
Baixa resistência e produtividade: um problema recorrente
É neste ponto em que a mineradora enfrentava problemas: quando rochas lamelares passavam direto pela abertura máxima do britador de mandíbulas. Quando tal situação ocorre, alguns matacos atingem a correia transportadora em cheio.
A concentração de carga na extremidade de contato rasgava a correia. Pior do que isso, algumas rochas ficam presas nessa posição e com o motor movimentando a correia continuamente, o rasgo se alastrava de forma descontrolada.
Como a correia afetada tem apenas 30 metros de comprimento, em alguns casos não havia tempo de parar a operação antes da perda total da correia. E não pense que tal ocorrência era rara. “Houve vezes em que o problema ocorreu até três vezes em um mês”, lembra o engenheiro responsável.
“As plantas de britagem são sequenciais. Ao parar um transportador, todo o processo para”, pontua.
Portanto, neste caso, além da segurança, resistência e produtividade devem andar juntas. Pois, em casos de paradas, a operação era interrompida, havia perda de produção, custos de manutenção e riscos de acidentes com os trabalhadores.
Trabalho em conjunto com a Mercúrio
Com mais de uma década de experiência na operação, a equipe de manutenção sabia da severidade da aplicação da chamada correia de sacrifício. “Não seria uma correia tradicional que resolveria o problema”, conta.
A necessidade não era exatamente por um produto que não rasgasse, mas que evitasse o alastramento do dano ao longo da extensão. Além disso, era imprescindível que pudesse ser emendada a frio.
A peculiaridade do caso levou o cliente a acionar seus fornecedores, mas só a Mercúrio aceitou o desafio. “O pessoal da engenharia da Mercúrio esteve na planta para identificar o problema e as características da operação”, salienta o responsável.
Nosso objetivo era apenas um: aumentar a resistência e produtividade da operação.
Num trabalho totalmente orientado ao cliente, o desenvolvimento da solução envolveu a Engenharia de Manutenção, a Equipe de Supervisão de Transportadores de Correia do cliente e a Mercúrio.
“Unimos experiências para desenvolver algo diferente porque sei da capacidade técnica tanto nossa, quanto da Mercúrio”, afirma o engenheiro.
Solução personalizada para mais resistência e produtividade
Como primeira tentativa, além do uso da cobertura MercoRip, mais resiliente e resistente a impactos e rasgos, uma malha de aço, Rip Proof, foi inserida na cobertura superior. Sua função é aumentar a resistência ao movimento no caso de um mataco atravessar a cobertura. Assim, um sensor verifica a sobrecarga na corrente e desarma o motor, evitando o alastramento do rasgo.
Na prática, ao ser atingida por uma rocha lamelar 30 dias depois da instalação, a correia parou apenas depois de 17 metros, lembra Alexandre Lacerda, então engenheiro da Mercúrio. “Os danos foram significativos e exigiram a troca total”, conta. Além disso, “o cliente precisava de resistência mínima de um ano”, lembra ao citar o desafio.
Identificado o problema e desenvolvida a solução, iniciou-se o segundo teste, novamente comprometido por um rasgo. Dessa vez na borda, pois a largura do Rip Proof era menor do que a da correia. “Voltamos para o projeto e melhoramos mais ainda a correia”, diz Lacerda.
Dessa vez, além da malha de aço cobrindo a largura total, foi inserida uma lona de aramida com a função de atuar como breaker. Isso aumentou a resistência a rasgos e, caso ainda assim eles ocorressem, o Rip Proof reduziria a extensão do dano. “Fizemos uma correia bem robusta e apropriada para este tipo de aplicação”, comemora o cliente.
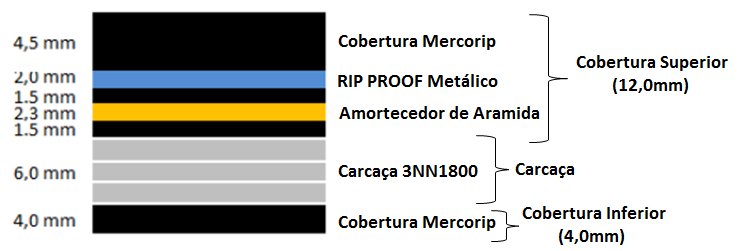
Os resultados de um trabalho em equipe
Instalada em janeiro de 2017, a correia foi um sucesso absoluto mesmo com o britador trabalhando com abertura máxima e permitindo a passagem de maior quantidade de matacos. O equipamento trabalhou por 13 meses consecutivos até fevereiro de 2018. “Ela não rasgou, mas trabalhou tanto que a cobertura superficial desgastou de forma natural”, avalia o engenheiro responsável.
De fato, resistência e produtividade eram indispensáveis para as operações da mineradora.
Como consequência de um intenso trabalho de engenharia orientado ao cliente e desenvolvido a quatro mãos, o resultado se disseminou. “Replicamos o conceito para outros transportadores e outras minas”, conta o gerente de manutenção, que apresentou o case em seminários internos da empresa.
O sucesso é tão evidente que os cerca de 40 a 50% de custo adicional em relação à solução convencional são absorvidos pela maior confiabilidade da planta. “O pessoal de campo fica surpreso com a resistência e durabilidade. Chegamos a um conceito que funciona”, comemora o cliente.
Para Lacerda, se trata da correia mais resistente oferecida pela Mercúrio atualmente e que, por isso, apresenta uma relação entre custo e benefício indiscutível. “Ela se paga em comparação à quantidade de correias que teriam de ser compradas e por evitar paradas”, diz.