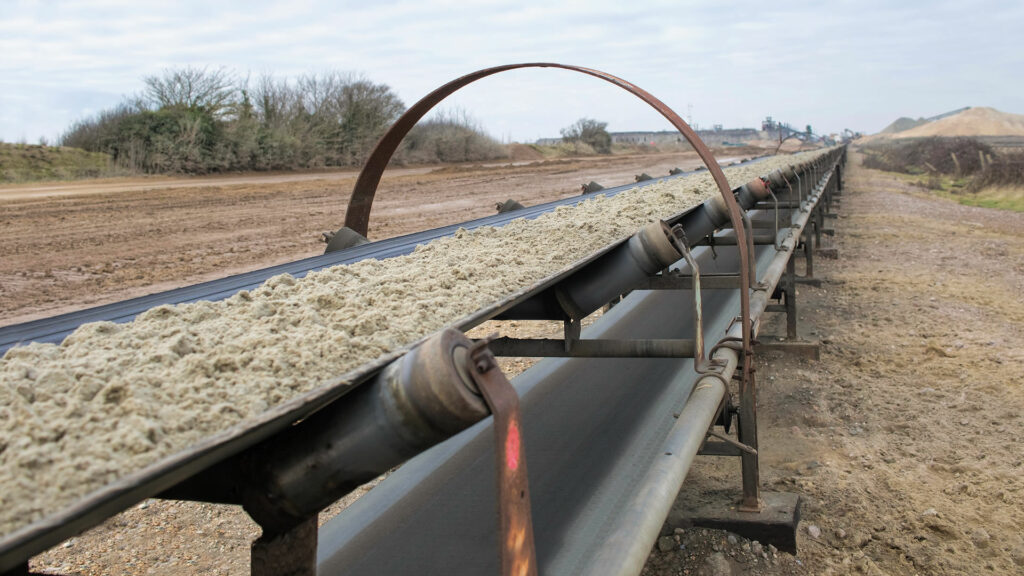
Often attributed to scientist Albert Einstein, the phrase “God is in the details” is an interpretation of a well-known passage from the Hebrew Bible, the Parasha Mishpatim. The phrase perfectly illustrates how a detail can, for example, be fundamental to separating the success and failure of a project.
In the case that we are going to bring you today, the rollers were fundamental to define the success or failure of this project.
In 2017, Fospar, the only phosphate fertilizer industry in the state of Paraná, contacted Mercúrio to manufacture a conveyor belt to replace the belt that was in operation.
Located in the city of Paranaguá, with its own port terminal in the city’s port, one of the most important in Brazil, Fospar accounts for around 10% of the national production of this important agricultural input.
Aware of the undertaking’s responsibility to manufacture a belt capable of transporting simple superphosphate – a type of fertilizer that reaches a temperature of 150º C –, in September 2017, Mercúrio delivered to the customer the CT ABT 4EP 2200 80” conveyor belt. x 105m.
“From our experience, it was the ideal model to work during the period of 12 months, according to the client’s expectations”, recalls Oséias Neves Boaventura, responsible for the commercial service of the client, who, at the time, worked in the Engineering and Mercury Technical Assistance.
Surprisingly, after about 3 months of its installation, Hosea was informed that the belt was showing great localized wear. A history that also occurred with previous belts from other manufacturers.
“When we noticed the problem, the impression was that that belt would not be able to operate during the scheduled period and we contacted Mercúrio”, says Jorge Stachoviak, Fospar’s Warehouse Manager.
Understanding the case
Faced with the urgency of the situation, Oséias scheduled a series of monthly technical visits, the first being held in early December 2017. “At Fospar, I could see that the belt had superficial cracks, which are normal, due to the peaks of temperature that occur during the process. However, fatigue lines appeared early in the lower and upper coverings”, he recalls.
The fatigue lines, explains Boaventura, are deeper marks of wear that deform the belt, compromising its operation. In some cases, these marks end up exposing the carcass causing direct contact with the transported material.
Thanks to the experience acquired in years of work in the Engineering and Technical Assistance area, in the first visit, Oséias was able to identify the cause of the premature wear of the belt: the same one that caused the great damages in the previous belts.“
After a lot of analysis, I noticed that the problem was not the belt itself, but some other components of the equipment that were not operating as intended. More specifically, the positioning of the load stand’s central roller”, he says.
Conveyor Belts rollers: Millimeters that make the difference
The rollers are fundamental parts for the perfect functioning of the belt, preventing or delaying the appearance of fatigue lines. However, an unevenness of about 50 millimeters in the easels was causing the central roller, precisely responsible for preventing the early appearance of fatigue lines, to press the belt, providing the appearance of these lines and double deformation.
The condition was further worsened by the high temperatures of the load being transported, which naturally hardens, ages and self-vulcanizes the belt’s rubber.
“With the more rigid rubber, it loses its mechanical property and its elasticity. This condition, added to the atypical situation in the equipment, generated a mechanical action, disturbing its normal operation, accelerating wear, cracks and breaks in the belt”, explains Oséias.
To correct this occurrence, a change in the structure of the load stands was suggested.
Following the technical guidelines, the customer raised the height of the central roller, without having to change it.
According to Hosea, “the guideline was to raise the central roller by 50 millimeters to eliminate contact with the corner of the side rollers. Thus, the rollers would be leveled and the belt would pass over them, without contacting the corner of the roller”.
A deviation of 5 centimeters was the cause of the fatigue that was prematurely damaging the conveyor belt.
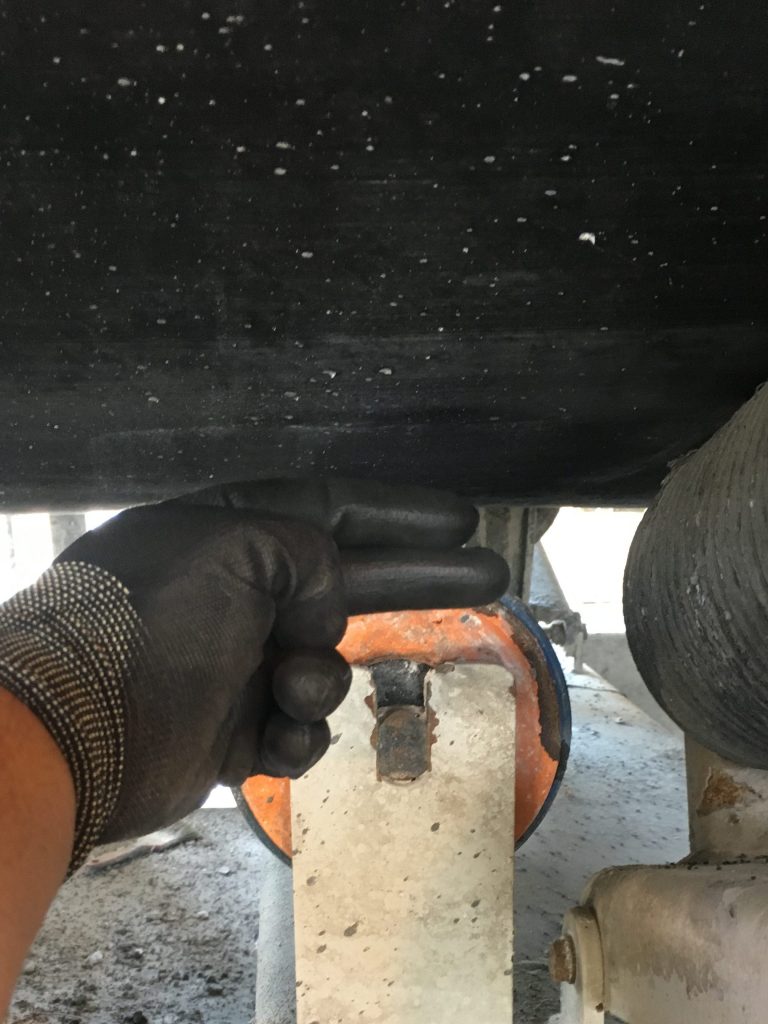
The accurate diagnosis completely changed the scenario.
“It’s the details that make all the difference. With experience, we learned that the belt ‘tells’ us what is happening to it. We have to be attentive to know how to interpret and make the correct diagnosis”, teaches Hosea.
Quality and reliability are non-negotiable
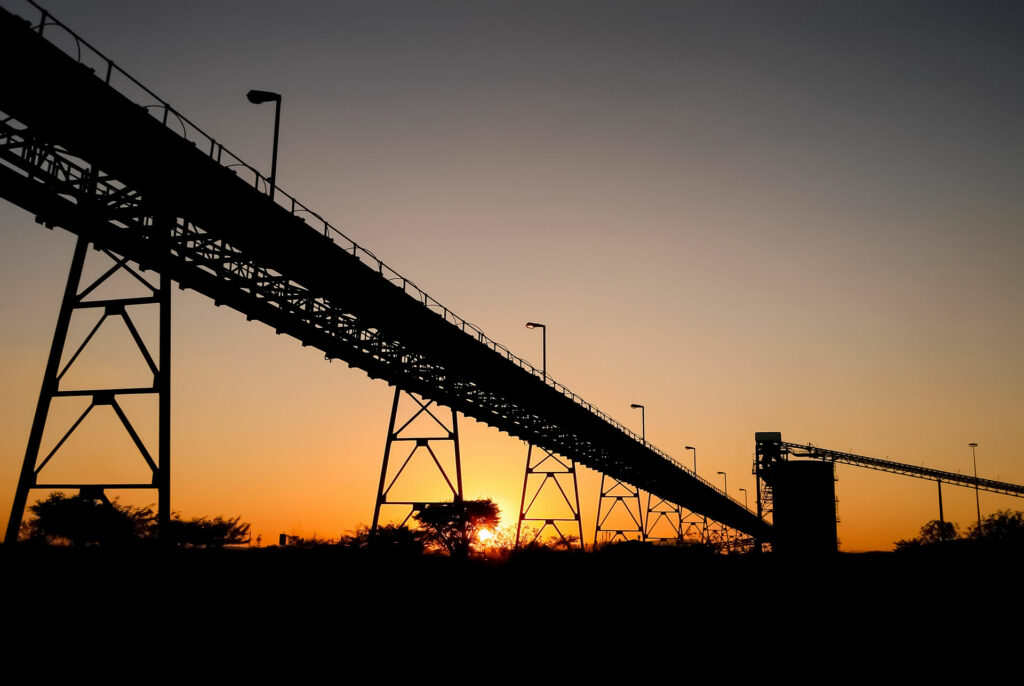
As a result, the adjustment in the structure of the easels, in addition to avoiding the replacement of the conveyor belt, guaranteed its useful life for 17 months, that is, 5 months longer than the initial forecast.
“Monthly monitoring was essential not only to adjust the belt’s operation, but also to extend its useful life. The knowledge and experience of Mercúrio’s service gave us all the confidence to postpone the belt change”, emphasizes Stachoviak.
In February 2019, Mercúrio replaced the belt at Fospar. With the adjustment made to the easels, the initial forecast is that the new belt will be able to operate for 2 years, without surprises and in complete safety.
Check out the before and after of the belt alignment below.

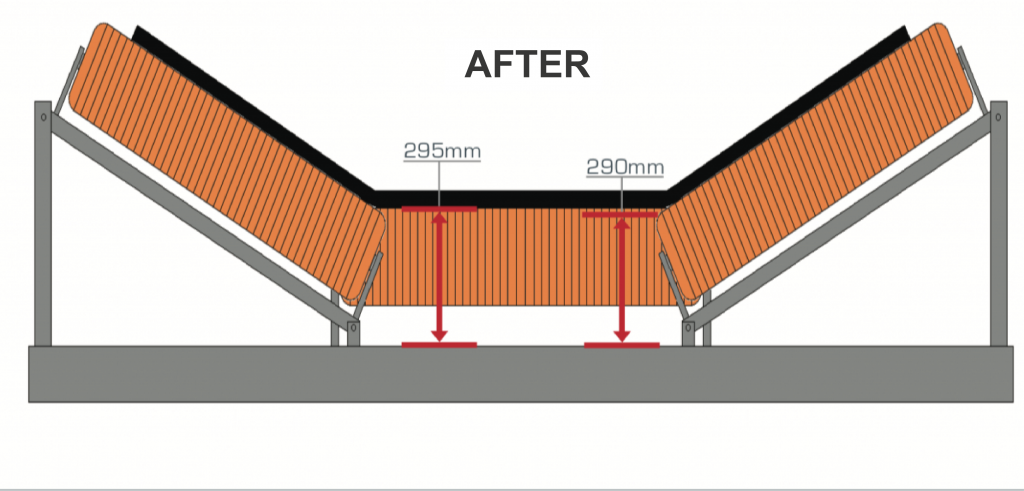