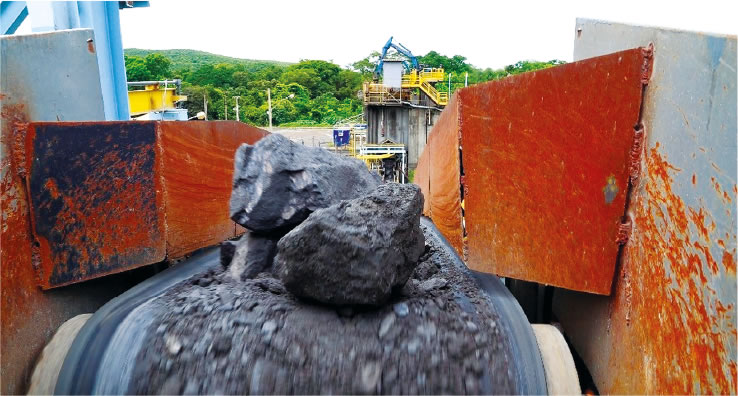
Using the right conveyor belt in your operation can bring significant savings and reduce maintenance downtimes. Below we share a success case with the AngloGold Ashanti mining company that after adopting the use of an aramid conveyor belt has seen a significant increase in the savings and productivity of its operations.
The Serra Grande Unit of the AngloGold Ashanti mining company located in Crixás, Goiás, and a Mercurio customer, uses conveyor belts in its extraction operation of quartz, dolomite, and graphite shale in an underground mine.
The material being mined has high granulometry, a lamellar shape, and the presence of cutting material. As Mercurio’s Account Manager David Souza recalls, this is a “very raw ore that feeds the entire crushing sequence”.
In one of the periodic visits that Mercurio’s team makes to customers, Souza identified a critical point in the mine’s operation. “What called my attention was how often they would change the product, every eight months for normal wear or even less when tears occurred,” was the comment about the belt that receives the ore being taken from the mine. “As this is a high-cost product, I took the case to our technical team to evaluate and develop a solution,” he shares.
After all, in addition to the cost with the belt, the constant interruptions for maintenance or changing the belt out due to total loss resulted in many hours of downtime, thus decreasing productivity.
Solution with an Aramid conveyor belt
The Mercurio Aramid Belt is named after the textile used in its composition. It is a material five times stronger and five times lighter than steel. That is why its properties of resistance to tension, weight, and stretching are much higher.
Its performance is so impressive that it can even replace steel belts in some applications. When it really shines though is mainly in severe applications such as that of the Serra Grande mine. In these situations the aramid belt is efficient against tears and ruptures and is capable of absorbing high impacts.
Because it is an extreme operation, there was only one incident during this period that caused slight damage to the belt, but with much less severity than in the past. There was a scheduled downtime for repair that, after following Mercurio’s guidance, eliminated the problem.
So the customer was very pleased with the savings in resources, time, and labor. “They saw gains in operational safety, reliability, as well as in savings and productivity. They no longer allocate operators to maintenance”, Souza points out.
The result was so satisfactory that AngloGold Ashanti went on to use the aramid solution in other applications. The product showed very good performance mainly in places with material of larger granulometry with a great cost-benefit advantage.
In addition to being more durable, the aramid belt is lighter, so it demands less energy to be driven. The customer’s estimated savings reaches 8%, which made it possible to change the motor from a 30 HP to a 25 HP motor.
An investiment tha brought savings and productivity
In relative terms, considering only the acquisition costs, the aramid belt represented a higher disbursement compared to the previous solution.
But over the more than 36 months since it started operations, the aramid belt has already delivered more than R$ 1.2 million in savings for Anglo-Gold Ashanti. The gains go beyond the cost with the belt itself: the customer stopped performing two stops a month, gaining with savings and productivity.
After all, since the aramid belt does not need to be changed every eight months, the acquisition cost has been absorbed. AngloGold Ashanti also stopped disbursements with maintenance and kept the operation running.
For the customer, the experience has been very rewarding even though at first they were fearful with the low thickness of the belt offered, which only has one ply, different from the previous specification with three plies. Once installed though, the customer has proven the actual performance of aramid, which does not get misaligned, has very low dilation, and is highly resistant..
Estimated monthly espenses eliminated with the Aramid belt
Maintenance | Monthly amount | Months | Total amount |
Materials | R$ 13.040,00 | 36 | R$ 469.440,00 |
Labor | R$ 22.400,00 | 36 | R$ 806.400,00 |
Total savings | R$ 1.275.840,00 |