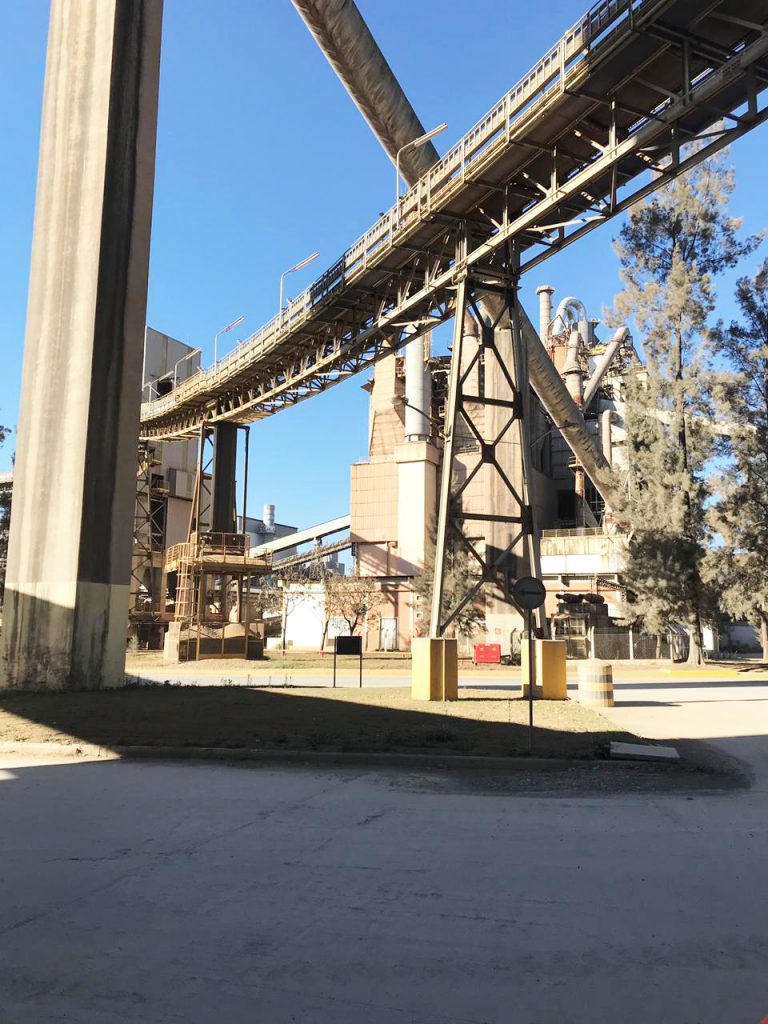
Vista exterior de la Unidad Barroso de LafargeHolcim.
El dicho popular enseña que “agua goteando en piedra dura, golpea y golpea hasta romperla”. Bueno, fue con este pensamiento en mente que el equipo de Mercurio logró, con gran esfuerzo, realizar otro Caso de Éxito más para la empresa: brindar una importante correa transportadora tubular de lona LafargeHolcim para generar mayor productividad y reducir los gastos del cliente, consolidando así la asociación y la relación de confianza.
LafargeHolcim es líder mundial en materiales y soluciones para la construcción, con presencia y cobertura a nivel nacional. En Barroso, en el interior de Minas Gerais, la empresa opera una de las mayores productoras de cemento y agregados de Brasil.
“Después de varias visitas a la planta, presentando los diferenciales de Mercurio y mostrando cuánto podíamos agregar al negocio, logramos producir el informe que detallaba las fallas y anomalías de una correa transportadora fabricada por un competidor”, recuerda Ivo Genelhu de Souza, entonces responsable por la atención al cliente en Mercurio.
Y no era una correa transportadora común, sino la primera correa transportadora tubular para el transporte de cemento en Brasil desde el molino hasta los silos. En otras palabras, su importancia es enorme para la operación de la fábrica y su parada resulta en la paralización de toda la operación, generando muchas pérdidas para el cliente.
Según el informe de LafargeHolcim, de junio de 2019, la correa de más de 700 metros de longitud presentaba un gran desgaste, con varias fisuras a lo largo del equipo. En estas condiciones, la correa, que fue diseñada para una vida útil de aproximadamente 4 años, debía sufrir cambios recurrentes de alrededor del 30% de su cuerpo cada 2 años, además de 4 empalmes que presentaban problemas críticos, amenazando con romperse en cualquier momento.
En este escenario, la tarea de Correas Mercurio fue bastante desafiante: aumentar significativamente la vida útil, reduciendo los gastos del cliente en empalmes, además del monitoreo constante del desempeño de la correa, con informes periódicos.
Estudio de campo para desarrollar la mejor solución
Luego de analizar el historial enviado por la empresa, Mercurio realizó visitas a la fábrica para monitorear el funcionamiento. A partir de esos análisis, fue elaborado un informe por los equipos Técnico y Comercial de Mercurio con el diagnóstico, soluciones sugeridas, plazos de entrega, instalación y costos.
“En una de estas visitas, junto a nuestro entonces Asesor Técnico, Iván Vitor de Souza, realizamos una nueva inspección, aún más exhaustiva, y analizamos el producto en nuestro laboratorio de Jundiaí”, recuerda Ivo.
Otra información importante investigada por Mercurio fue el tipo de material transportado. El cemento sale del molino y entra en contacto con la correa a una temperatura promedio de 100°C. Expuesta a altas temperaturas, la correa se deteriora más rápido.
Diagnósticos y resultados para implantar una correa transportadora tubular
Con toda la información necesaria, el equipo presentó al Supervisor de Planificación de LafargeHolcim, Victor Luiz Pereira de Moura, y al Gerente Corporativo, João Amaral, el diagnóstico definitivo: resecamiento de la correa y grietas en sentido longitudinal en toda su extensión y en las enmiendas, provocadas por la alta temperatura del cemento transportado.
Para solucionar este problema se planteó la siguiente: solución: una correa transportadora tubular con cubierta AT (alta temperatura), reemplazando a la EA (Extra Abrasión) de la competencia. “La especificación de cubierta EA puede soportar una temperatura máxima de 80°C, mientras que la AT de nuestro portfolio, ideal para transportar materiales más abrasivos, puede soportar temperaturas mucho más elevadas, como en el caso del cemento transportado por la correa”, explica.
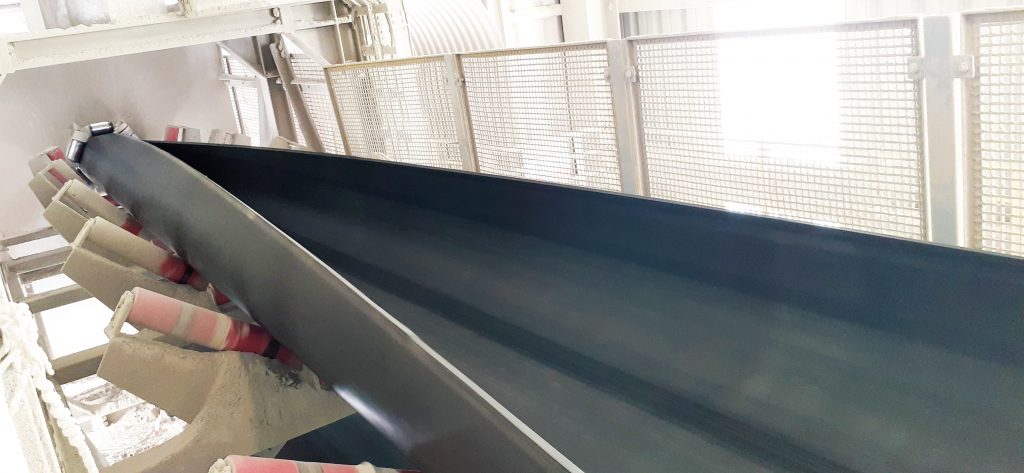
Además del cambio en la especificación, Mercurio también sugirió un aumento en el espesor de la cubierta superior, reforzando aún más su protección contra las acciones del material transportado a lo largo del tiempo.
Como complemento, otra modificación sugerida fue la disminución del número de empalmes de cuatro a uno solo. Así, además de prevenir la aparición de fisuras, la reducción del número de empalmes representa una importante reducción de costos operativos y de mano de obra para el cliente.
Con todos estos ajustes, la correa transportadora configurada y proporcionada por Mercurio presentaría una expectativa de vida de 6 años, frente a los 4 años de la correa anterior, y así un aumento del 50%. Además, con los cambios sugeridos, ya no sería necesario cambiar el 30 % de la correa cada 2 años. Otra diferencia importante fue la reducción del número de paradas para cambio de empalmes, asegurando una mayor productividad en la fábrica.
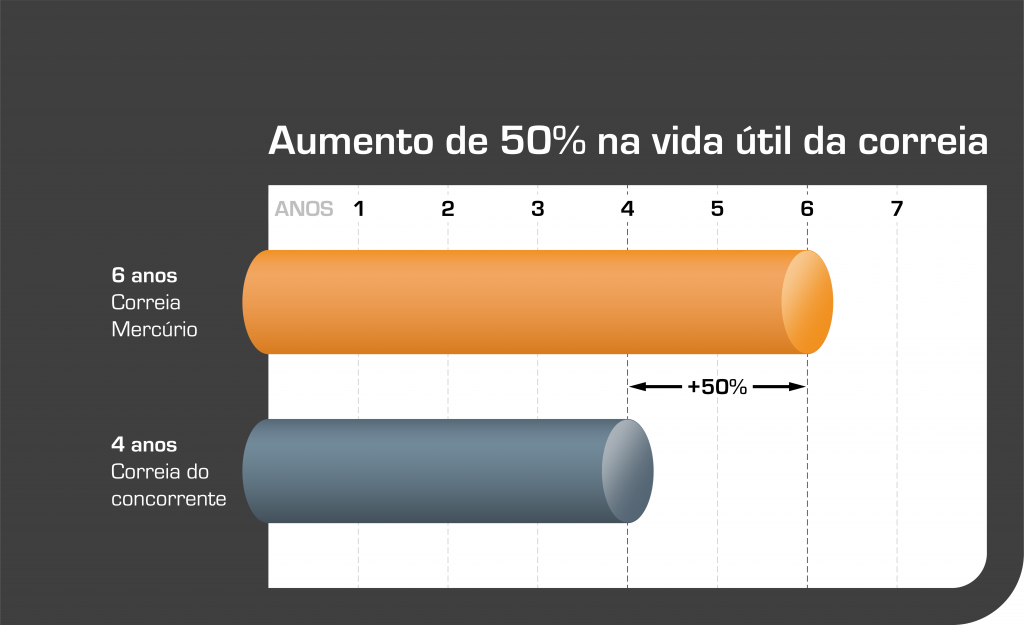
Comparación de la correa transportadora tubular Mercurio con la competencia.
Resultados increíbles y satisfacción garantizada
Luego de presentar el informe completo con todas las ventajas, beneficios y expectativas de desempeño, en enero de 2020 LafargeHolcim instaló la correa transportadora tubular proporcionada por Mercurio, en lugar de la correa problemática.
Desde entonces, el desempeño de la correa ha cubierto con éxito todas las expectativas depositadas.
“Estudios fundamentados, presentados en varios informes producidos por nosotros, demuestran el excelente desempeño. Estamos muy satisfechos con los primeros resultados y somos optimistas con respecto al aumento de la productividad y la reducción de costos para la fábrica”, celebra Victor Luiz, Supervisor de LafargeHolcim, Unidad Barroso.
Tales resultados se comprueban en las visitas periódicas que realiza Ivo junto con el equipo técnico de Mercurio. “Cada 60 días, en promedio, realizamos inspecciones detalladas para monitorear el desempeño, con medición de dureza, medición de temperatura y demás informaciones relevantes que se actualizan en informes detallados enviados al cliente”, refuerza Ivo.
“Estamos muy satisfechos no solo con la solución presentada por Mercurio, sino principalmente con el nivel de participación de todo el equipo. La atención durante el proceso, desde las primeras visitas al seguimiento de la instalación y ahora las visitas periódicas para comprobar el funcionamiento de la correa, nos deja mucho más tranquilos y demuestra que tomamos la decisión correcta”, afirma Víctor.
Este caso de éxito abrió las puertas a nuevos proyectos de Correas Mercurio en LafargeHolcim, así como otro suministro de correas para la planta de Barroso y otra correa para la planta de Pedro Leopoldo, también en Minas Gerais.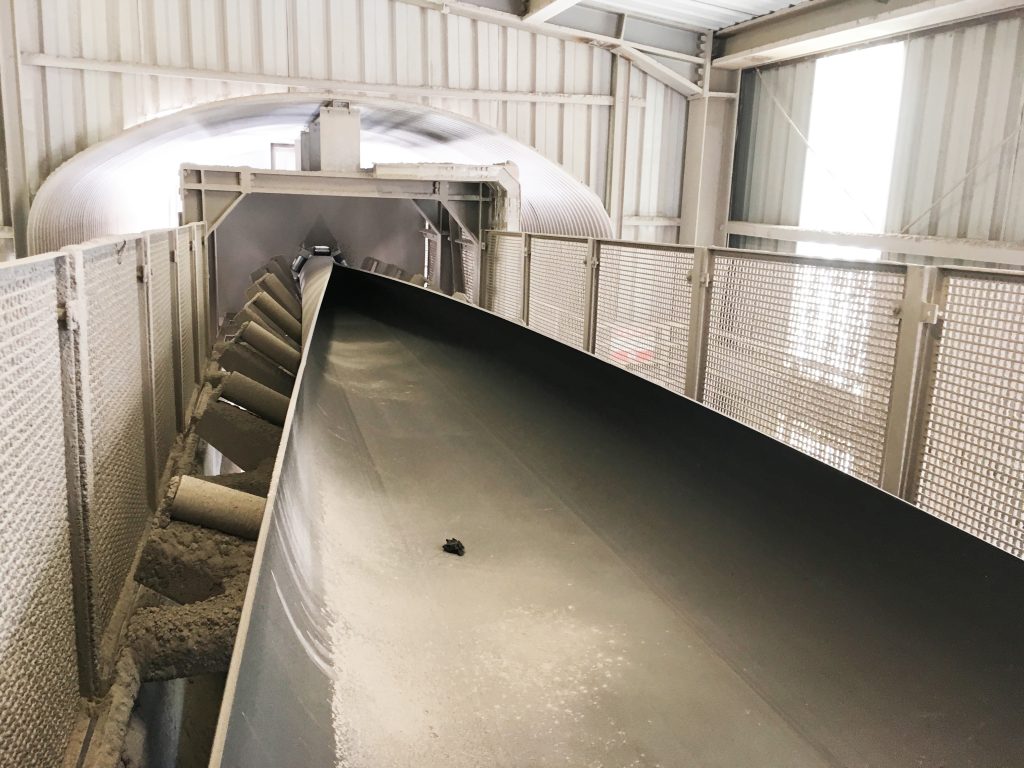
Con cubierta AT (Alta Temperatura), aumento del espesor de la cubierta superior y disminución del número de empalmes, la Correa Transportadora Tubular de Mercurio exhibe una expectativa de vida útil de 6 años y una reducción significativa de las interrupciones.