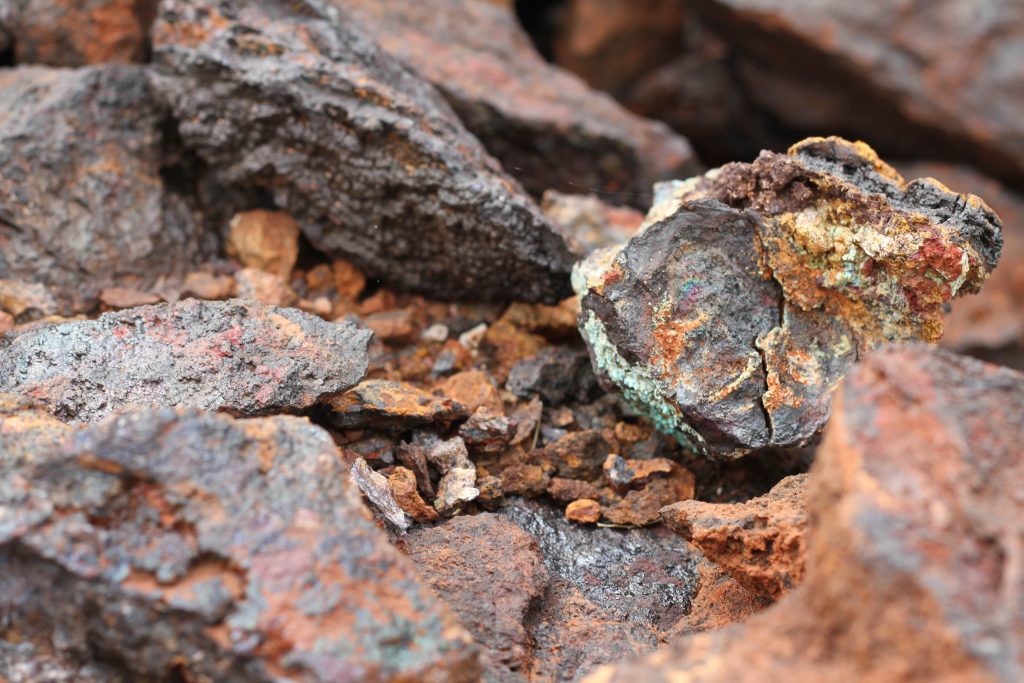
Mineral de cobre: utilizado en la generación y transmisión de energía y en equipos electrónicos, es el 3º mineral más consumido en el mundo y posee un alto índice de abrasividad.
Detrás solo del hierro y el aluminio, el cobre es uno de los metales más utilizados en el mundo, siendo muy común en la generación y transmisión de energía, además de estar presente en prácticamente todos los equipos electrónicos.
Fue en la ciudad de Marabá, región sureste del estado de Pará, que una de las minas de cobre más importantes del país, subsidiaria de la mayor compañía minera de Brasil, contactó a Mercurio solicitando una correa transportadora que sea suficientemente resistente para transportar un mineral muy importante.
A finales de 2018, en una de sus visitas a este importante cliente, Alejandro Lacerda, entonces Gerente de Cuenta, y Fernando Asís, en ese momento Coordinador del Área de Ingeniería de Aplicaciones y Asistencia Técnica de Mercurio, fueron recibidos por el equipo de Ingeniería de la mina con un pedido especial: extender la vida útil de una correa transportadora.
Pero no se trataba de una correa transportadora cualquiera.
El TR 2010-01 es un transportador cerrado y reversible (que opera en ambos sentidos), responsable de la operación de todo el proceso productivo de la planta y su parada implicaba la paralización general de la fábrica, incluyendo maquinaria y personal, lo que representaba un impacto directo en la producción.
Este fue un desafío que requirió un esfuerzo conjunto entre las áreas de Ingeniería y Asistencia Técnica y Comercial de Mercurio para poder encontrar a la vez la mejor solución técnica para el caso, con costo y plazo que atendieran a las necesidades del cliente.
Gracias a la naturaleza del cobre, su alta abrasividad agredía la correa transportadora, que presentaba desgaste en la cubierta en hasta tres meses. Por esta razón, se programaba la Parada General de la Minera, haciendo que, obligatoriamente, las demás máquinas también tuvieran que pasar para revisiones y cambios, aunque se encontrasen en buenas condiciones de operación.
“Entre los transportadores y alimentadores de correa, hay alrededor de 50 equipos afectados por la paralización de este Transportador. Solicitamos el apoyo del equipo técnico de Mercurio para que viabilice una solución que permitiera mayor vida útil del equipo y, de esa forma, ampliar el período entre paradas programadas”, recuerda Renato Caverzan, Ingeniero Responsable de los Transportadores Correa de la minera.
Análisis y diagnóstico de las correas transportadoras
“Nuestro desafío era encontrar una solución que aumentara la vida útil de la correa y, en consecuencia, redujera el número de paradas anuales de la planta, sin generar más costos para el cliente”, explica Fernando Assis.
Basado en un informe técnico realizado utilizando ultrasonido, el equipo mapeó el desgaste en la cubierta superior. Fueron mapeados 17 puntos en la dirección transversal, cubriendo todo el ancho de la correa, lo que permitió determinar y proyectar su vida útil.
La durabilidad de la correa transportadora, con respecto a resistencia a la abrasión, está directamente relacionada con el espesor, el tipo de revestimiento y el tipo de material a ser transportado.
Con la información revelada por el ultrasonido, se realizaron análisis de Ingeniería, con el objetivo de proponer la alteración necesaria para aumentar la vida útil de la correa de especificación CT EAS 5PN4000, un modelo pesado, con cinco lonas de Nylon Poliéster y cubierta EAS con resistencia a la abrasión máximo 70 mm 3.
Assis recuerda que “por ser un material muy abrasivo, éramos conscientes de la necesidad inicial de cambiar la cobertura a una que ofreciera mayor resistencia a la abrasión. Sin embargo, un aumento en el espesor de la cubierta superior impactaría naturalmente en el aumento de masa (peso), requiriendo mayores esfuerzos en el accionamiento del transportador”. Entonces, para evitar este desgaste en la correa, el equipo de Mercurio realizó un estudio de las tensiones actuantes con el objetivo de posibilitar la alteración de la carcasa, reduciendo su peso, en contraposición al aumento del espesor de la cubierta.
Ante todas las posibilidades planteadas, el equipo Mercurio presentó al cliente la solución que, según pruebas realizadas en el laboratorio de la empresa, podría aumentar la vida útil de la correa transportadora de mineral: una nueva cubierta mucho más resistente, la XEAS (X Extra Súper Abrasión), combinada con un nuevo tipo de carcasa, la 4PN4000.
“En la práctica, hemos aumentado mucho la resistencia a la abrasión de la cubierta superior que pasó de 70 mm 3 a 30 mm 3. Además, aumentamos el espesor de 12 mm a 18 mm, un aumento del 50%, y quitamos una lona de la carcasa, lo que representa una reducción de 2 kg/m2”, explica.
Solución eficiente y económica con cobertura y carcasa personalizadas
Tras el último cambio realizado en 2019, ya bajo la nueva especificación, el cliente comprobó el aumento de la vida útil de la correa transportadora de tres a casi cinco meses, incluso superior a los cuatro meses previstos inicialmente. Es decir, una disminución de cuatro a menos de tres Paradas Anuales Programadas, lo que representó un incremento significativo de más del 33% en la vida útil de la correa.
“Paramos para realizar el último cambio, ya con la nueva especificación, el día 15 de septiembre de 2019 y recién paramos de nuevo el 3 de febrero de 2020, es decir, casi 5 meses de vida útil. Y la correa aún tenía condiciones para seguir funcionado aproximadamente un mes”, resalta Caverzan.
También según el cliente, como la parada del transportador TR 2010-01 era responsable de la parada trimestral de mantenimiento de la planta, este cambio fue fundamental para generar mejores resultados, ahorros de gastos de mantenimiento, además de reducir la exposición de los empleados a riesgos de seguridad. “Y todo hecho con mucha agilidad. La proximidad de la fábrica de Marabá y la atención de todo el equipo de Mercurio facilitó aún más la operación, la logística de cambios y toda la atención necesaria”, expresó Daniel Tovar, Ingeniero de Mantenimiento del cliente.
Una solución eficiente y económica que, además de ser el responsable directo del aumento de la productividad de la planta de la empresa, se realizó con ajustes en la especificación de la correa, sin necesidad de grandes cambios de equipos, es decir, sin mayores inversiones.
“Siempre es un placer participar de desafíos de este tipo. Agradecemos al Ingeniero Renato Caverzan, responsable de los Transportadores de Correas, por desafiarnos en esta mejora, y por el gran resultado alcanzado con nuestros productos”, refuerza Alejandro Lacerda, Gerente de Cuentas de Mercurio.
“Sin dudas, este es un caso de éxito reconocido, tanto por la importancia estratégica del equipo como por la envergadura de la empresa. Y el resultado positivo solo se puede lograr gracias a la asociación y al trabajo mancomunado entre el cliente y Mercurio”, concluye Fernando Asís.