Considered one of the most modern and competitive pulp companies in the world, in 2016 Eldorado Brasil was looking for the best conveyor belt solution for transporting eucalyptus bark, a material that turns into biomass, generating energy to be used by the company itself and the market.
“Because of the characteristic of the load, we wanted a closed piece of equipment that would produce less volume of debris. We were also looking for a system that would use less idlers in order to have less maintenance costs,” explains Pedro Moraes, the Maintenance Coordinator for Eldorado Brasil.
Air system conveyor belt
The Air System Conveyor Belt soon presented itself as the ideal solution for this challenge as this belt works under an enclosed conveyor system and instead of sliding over idlers, it uses an air system for its movement, similar to floating.
Air is drawn from the atmosphere by an air suction machine and sent to a chamber. There it keeps a constant flow and pressure through orifices and is returned back to the atmosphere.
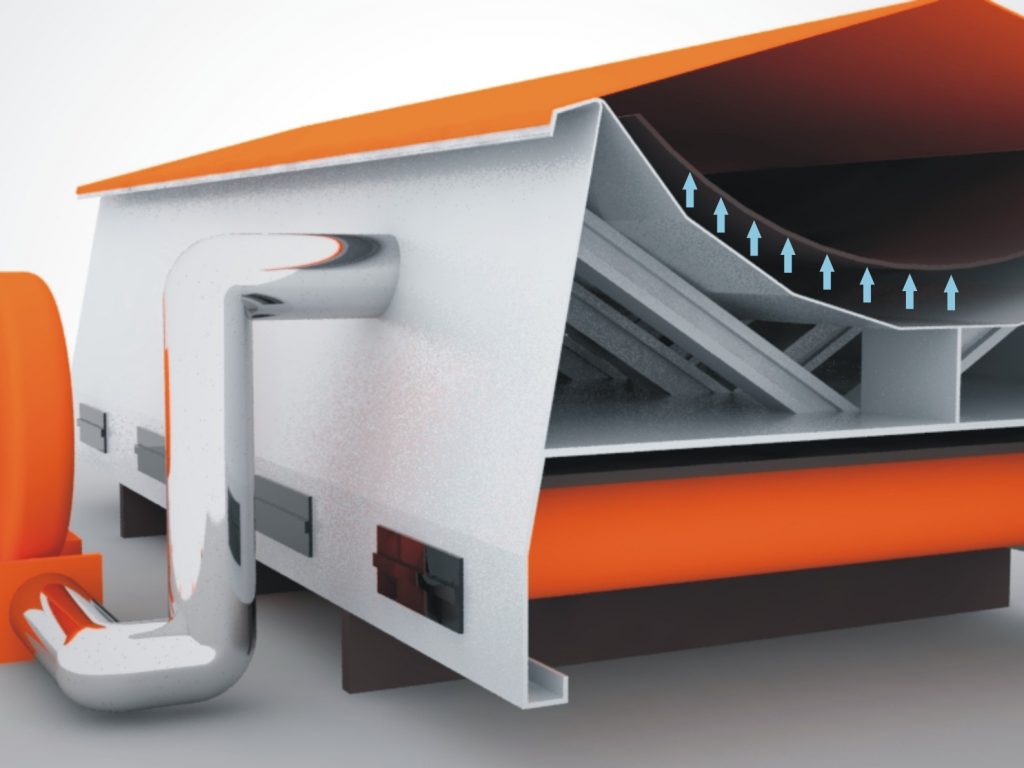
Along the path it generates a film between the belt and the trough, reducing friction.
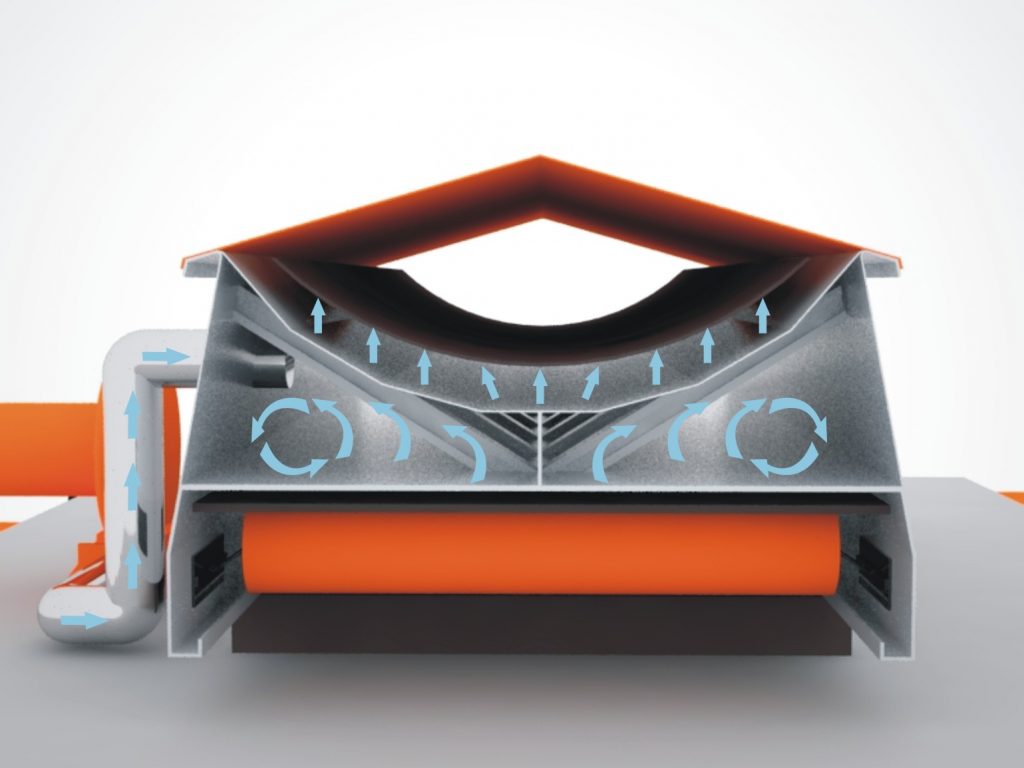
The reduced friction combined with trough design allows an even and regular transport flow, avoiding vibrations and belt deformation along the conveyor.
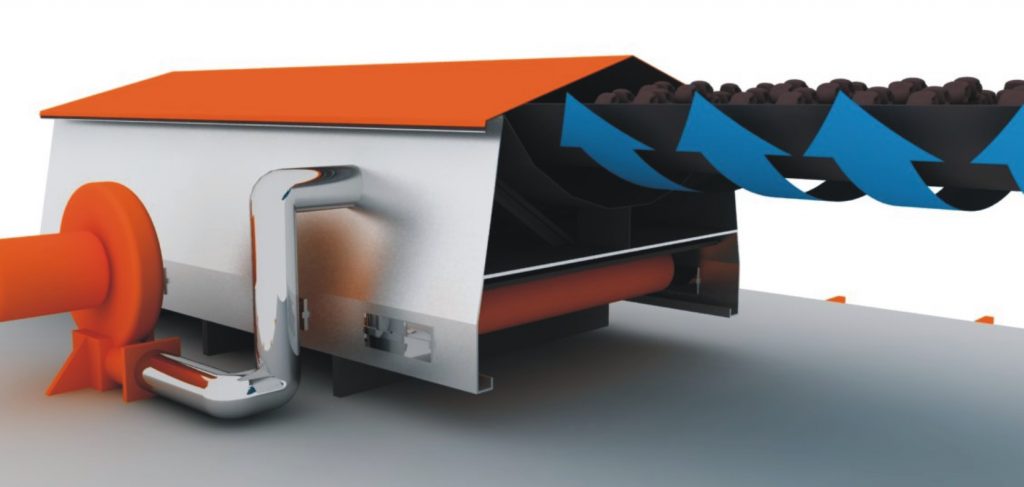
However, this belt model had never been produced in Brazil. Interested customers had to import the product, which ended up directly impacting two of the main problems for the industry: delivery time and high investment cost.
“This is where we decided to offer a new solution to Eldorado: develop the first Air System Conveyor Belt produced in Brazil,” says Ivan Vitor de Souza, Mercurio’s Technical Adviser.
A unique and customized national solution
A national leader in conveyor belt production, Mercurio brought together its team for an unprecedented challenge: nationalizing the production of this new conveyor belt model.
It would be a complex task involving several sectors in the company such as the product development team, quality management, laboratory, engineering, among others.
The first samples ended up not showing the result expected. Details such as the type of rubber that should be used, among other unique specificities involving the air system, required further studies and efforts by the team.
But the fact that it had never been done before and the complexity of the challenge did not shake the confidence of those involved. “Throughout the process, Ivan and Mercurio’s team gave the necessary support, making adjustments and corrections of routes, which left us confident with the final result,” says Pedro Moraes.
Once drawn from the atmosphere by an air suction machine, the air is sent to a chamber. At a constant flow and pressure, the air generates a film between the belt and the trough that raises it. The process reduces friction and prevents vibrations and belt deformations.
Specifications
Some of the challenges faced by Mercurio‘s team to reach the perfect Air System Belt Model were the type of carcass and strength class, the amount of plies, and the thickness of the upper cover.
“In the first attempt, for example, due to a concern with the life and longevity of the product, we used a type of cover with characteristics too high compared to the customer’s use. This ended up impacting the weight of the belt, making the model ineffective,” says Ivan.
After new stress and weight tests and adjustments made to the specifications such as the choice of the rubber for the type of cargo being transported, the company delivered the first Air System Conveyor Belt produced in Brazil at the end of 2016.
“We really worked hard to finally design the ideal model, just as the customer expected. We appreciate the trust of Eldorado Brasil, which has enabled us to demonstrate in practice that we can meet different customer needs and nationalize products that are outside our portfolio,” he says.
Quality, tradition, and confidence
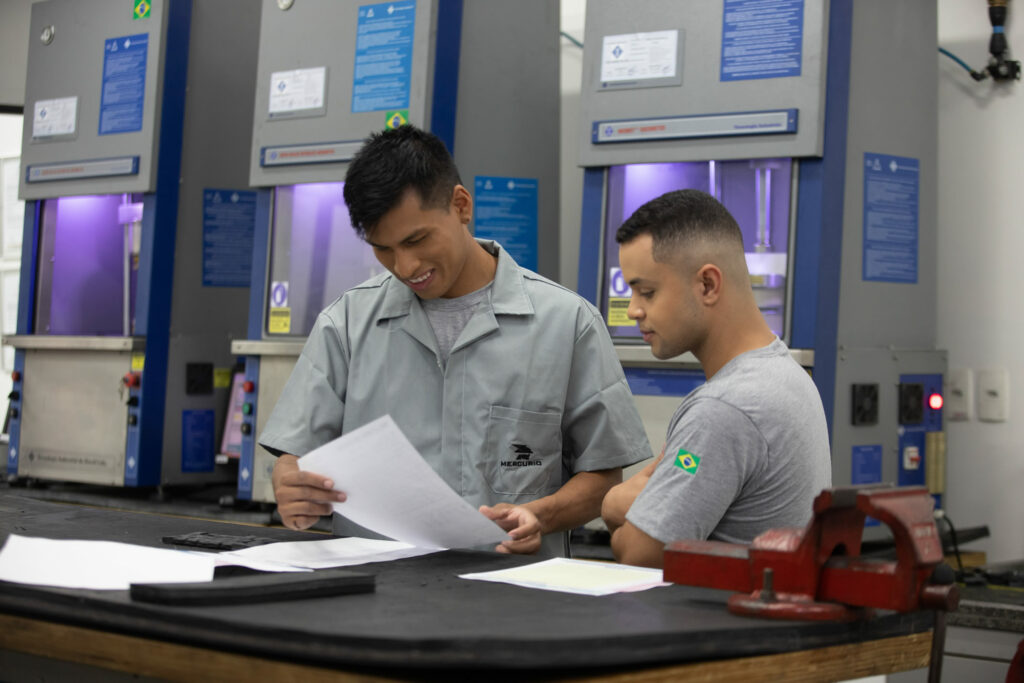
The result fully met the customer’s expectations. “We were fully satisfied. In addition to relying on full support from Mercurio, the result was excellent. Our partnership resulted in a product with a lower cost within a much shorter delivery time,” Moraes praised.
Now part of Mercurio’s portfolio, the belt makes up a system that is considered cleaner, agile, and easier to maintain compared to the traditional model. From this successful case, Mercurio has already produced and placed new models on the market.
Among the customers served is one of the largest global groups of cement and construction materials.
“The nationalization of the production of this conveyor belt was a milestone in the company. We are prepared to produce any kind of belt here in Brazil,” concludes Mercurio’s Technical Advisor.