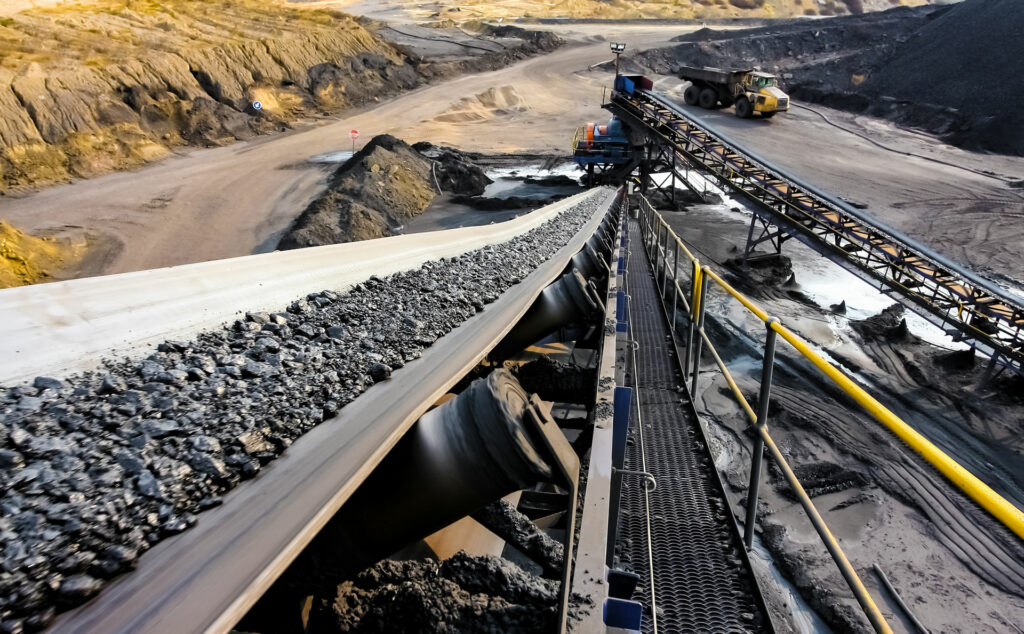
Responsible for an annual production of about 30 million metric tons of iron ore, one of the main iron mining units in Brazil located about 100 km from Belo Horizonte in the mining town of São Gonçalo do Rio Abaixo has three crushing plants. One of them, the so-called fine crushing plant, accounts for 15 to 20% of the minerals processed in the complex.
Resistance and productivity are essential in the production of mining companies. This is because its first stage of crushing receives rocks with a particle size of up to 300 mm that need to be fragmented until they reach the desired granulometry.
To do this, the ore is taken to a jaw crusher that makes the first fragmentation, and the work of this equipment is crucial for the operation because the rest of the line is prepared to work with smaller sizes.
Low resistance and productivity: a recurring problem
It is at this point where mining companies face problems when the lamellar rocks pass straight through the maximum opening of the jaw crusher. When this situation occurs, some large rocks hit the conveyor belt in full.
The load concentration at the contact end can tear the belt. Worse than that, some rocks can get stuck in this position and with the motor running the belt continuously, the tear can spread uncontrolled.
As the belt affected is only 30 meters long, in some cases there is no time to stop the operation before there is a total loss of the belt. And don’t think that such an occurrence is rare in this case. “There were times when the problem occurred up to three times in a month,” recalls the lead engineer.
“The crushing plants are sequential. When one conveyor belt stops, the entire process stops”, he points out.
Therefore, in this case, in addition to safety, resistance and productivity must walk together. Because in cases of downtimes, the operation is interrupted, there is loss of production, maintenance costs, and the risk of accidents with the workers.
Joint efforts with Mercurio
With more than a decade of experience in the operation, the maintenance team knew of the severity of the application of the so-called sacrifice belt. “It would not be a traditional belt that would solve the problem,” he says.
The need was not exactly for a product that would not tear, but that would avoid spreading the damage further. Moreover, it was imperative that it could be cold spliced.
The peculiarity of the case led the client to call upon its suppliers for help, but only Mercurio accepted the challenge. “Mercurio’s engineering personnel visited the plant to identify the problem and study the operation’s characteristics,” pointed out a lead engineer.
Our goal was singular: to increase resistance and the operation’s productivity.
In a task fully customer-oriented, developing the solution involved Maintenance Engineering, the customer’s Conveyor Belt Supervision Team, and Mercurio.
“We brought our experiences together to develop something different because I know our technical capability and Mercurio’s as well,” assures the engineer.
Customized solution for increased resistance and productivity
As a first attempt, in addition to using the MercoRip cover that is more resilient and resistant to impacts and tears, a steel mesh, Rip Proof, was inserted into the top cover. Its function is to increase the resistance to movement in case a large sharp rock passes through the cover. Then a sensor notices the current overload and disarms the motor, keeping the tear from spreading.
In practice, when struck by a lamellar rock 30 days after installation, the belt stopped only after 17 meters, recalls Alexandre Lacerda, Mercurio’s engineer at the time. “The damage was significant and required a complete belt change,” he says. In addition, “the customer needed a minimum resistance of one year,” he recalls when talking about the challenge.
Once the problem was identified and a solution developed, the second test was started, again compromised by a tear. This time on the edge because the Rip Proof width was smaller than the belt width. “We went back to the design and further improved the belt,” says Lacerda.
This time, in addition to the steel mesh covering the entire width, an aramid textile was inserted with the function of acting as breaker. This increased the resistance to tears, and if they were to occur, Rip Proof would reduce the extent of the damage. “We made a very robust and appropriate belt for this type of application,” celebrates the customer.
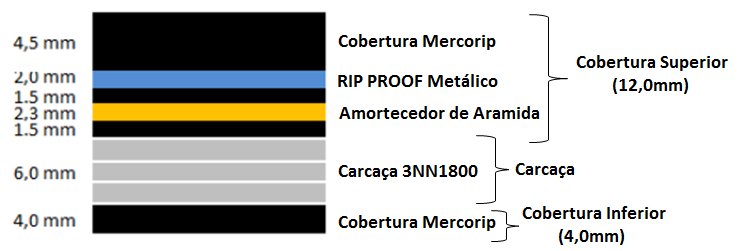
The result of teamwork
Installed in January 2017, the belt was an absolute success even with the crusher working with maximum opening allowing some larger rocks to pass through. The equipment worked for 13 months in a row until February 2018. “It did not tear, but worked so much that the surface cover had naturally worn out,” concluded the lead engineer.
In fact, resistance and productivity were indispensable for the mining operations.
As a result of intensive, foursome, customer-driven engineering work, the result was spread around. “We replicated the concept to other conveyors and other mines,” says the maintenance manager who presented the case in internal company seminars.
Success is so evident that the approximately 40 to 50% additional cost compared to the conventional solution is absorbed by the plant’s greater reliability. “The field personnel are surprised by the resistance and durability. We reached a concept that works,” celebrates the customer.
For Lacerda, it is the most durable belt offered by Mercurio today and because of that has an indisputable cost-benefit ratio. “It pays for itself when compared to how many belts that would have to be purchased and for avoiding downtime,” he says.