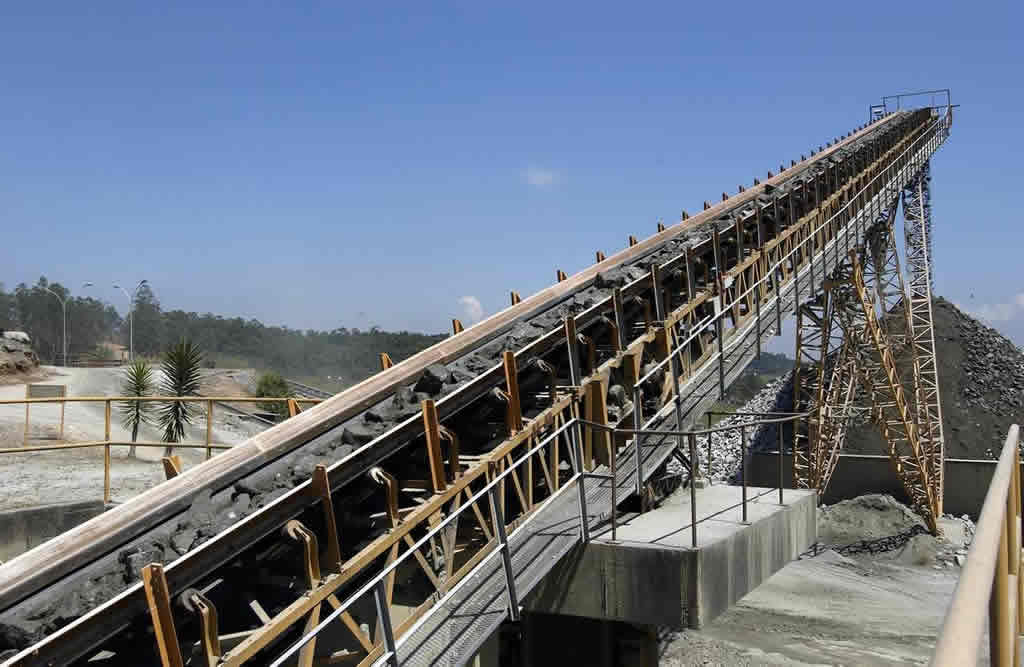
It is a fearful thing to have part of your production stopped for any company. After all, the durability and efficiency of operations are essential.
So imagine running the risk of seeing your entire line interrupted for a long period because a vital piece of equipment to the operation stopped working. So, until 2007, this was the case of the operation of one of the units of a large cement company in Brazil located in the State of Sergipe.
Durability and efficiency were indispensable in this case since the operation suffered from recurrent downtimes caused by problems with the steel cord conveyor belt that was used up to that time. When called on for support, the previous supplier could not provide a solution that met the company’s two needs.
To understand the size of the problem, this conveyor belt was the only one used to transport the material from the mine to the mixing yard. From this yard the materials are taken to the furnaces. The bottleneck is that this yard was able to store enough material for only 24 hours of operation.
If the problems with the belt used at the time were already having trouble with these conditions, they would worsen when the project was completed to increase production. The yard would have only 16 hours of operation without receiving material.
It was imperative to increase the durability and efficiency of the belt, which does not have redundant equipment, in order to increase the reliability of the operation. That is where Mercurio’s experience made all the difference.
UNDERSTANDING THE CASE
Manufactured and supplied by another company, the belt used at the time had low durability and efficiency. Tears and perforations were recurrent and because of the steel cords, any evidence of damage led to repairs that took a long time. Furthermore, due to the amount of splices, the maintenance cost was high and the operation had long downtimes.
Increasing the thickness of the conveyor belt had been the only solution proposed so far. However, there would be a cost to that. “It would lead to needing to change the drive assembly for more powerful motors, which has a higher acquisition value and would spend more energy,” points out Marco Túlio Viana, the Account Manager at Mercurio.
Due to the long partnership with Mercurio, the cement company asked us to develop a solution compatible with its needs, always taking into account the durability and efficiency of the belt, as Viana recalls.

So, even without knowing the history of the operation, Mercurio went to check out the situation. “Our Technical Assistance Manager went to the location to assess the conveyor belt’s situation and its problems, to then present a solution,” he says.
DURABILITY AND EFFICIENCY WITH A TEXTILE CONVEYOR BELT
The manager at the time was Dalton Clermont. “Our proposal was to replace the steel cord belt with a EP (polyester-nylon) textile conveyor belt manufactured by Mercurio,” he explains, referring to a product capable of withstanding severe conditions.
The arguments for the solution were that this material makes for an easier operation and withstands more rugged operations, says Clermont. Ultimately, if repairs are needed, the EP textile belt has a maintenance that is more financially and technically viable. Mercurio also offers a 5-year warranty on this material.
Against the proposal was the fact that the belt was a Long Distance Conveyor Belt as it was 2,800 meters long, also referred to as overland. In theory, usually steel cable belts tend to be more indicated for overland belts due to their risk of elongation. “Textile conveyor belts are usually indicated for shorter conveyor belts that are less subject to impacts or tears,” says Viana. While EP belts have a stretching index of 1.5%, for steel cord belts it is only 0.5%.
RELIABLE DURABILITY
Mercurio invested in a project to circumvent the risk. Calculations were made to determine the counterweight required to avoid stretching problems and the belt cover was increased from 6 mm to 8 mm. The heavier cover was compensated by reducing the weight of the carcass, since textile weighs less than steel. This way the same motors could continue to be used.
“It is necessary to have a very developed engineering and in-depth knowledge of both the product and the operation to reach a solution like this,” Viana points out.
Furthermore, neither maintenance nor the warranty were required. Mercurio’s first EP textile conveyor belt operated not for five, but for almost nine years. The second belt has been in operation for about three years and has no evidence of a problem. Neither of them require unscheduled maintenance. “We replaced a product that was having problems and brought a belt developed according to the customer’s demands,” says Clermont.
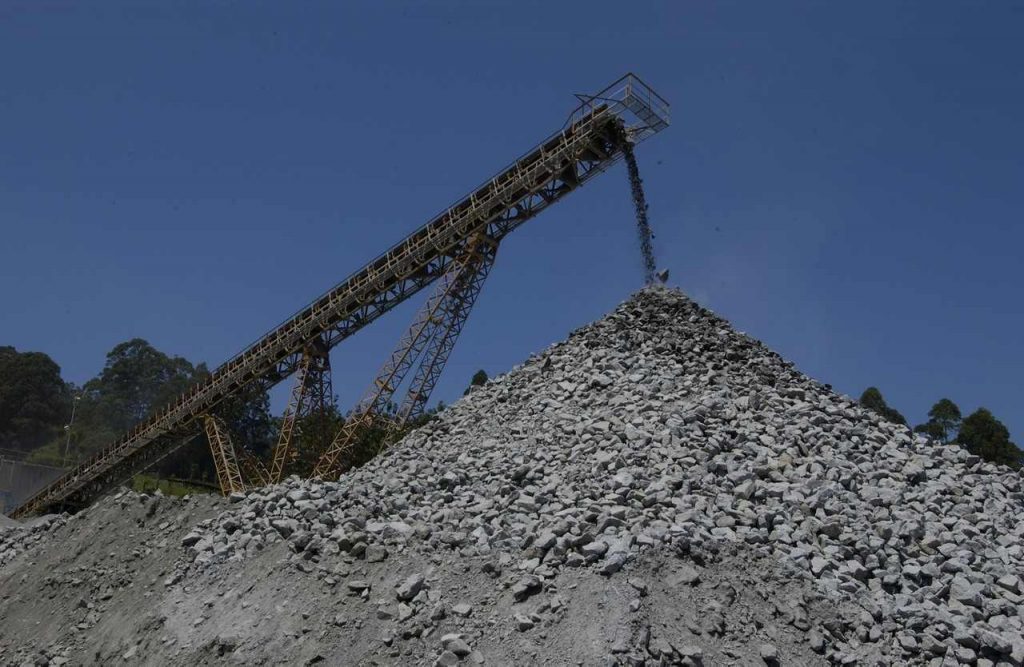
THIS MERCURIO SOLUTION BROUGHT SAVINGS OF ALMOST R$ 6 MILLION
In this context, the higher acquisition cost by about 50% was easily offset by the absence of maintenance, which cost the company approximately 30% of the cost of purchasing the previous belt.
In summary, we guarantee more durability and efficiency in the operations with Mercurio’s EP textile conveyor belt, as well as a reduction of around R$ 5.8 million over its nine years of operation and elimination of operating losses due to unscheduled downtimes.
ESTIMATED MONTHLY EXPENSES ELIMINATED BY THE EP TEXTILE CONVEYOR BELT:
Previous specification | Mercurio Conveyor Belt | |
Expected durability | 2 years | 9 years |
Acquisition cost | R$ 980.000,00 | R$ 1.471.000,00 |
Maintenance costs | R$ 320.000,00 | – |
Savings (R$) | – | R$ 5.850.000,00 |
Savings (%) | – | 450% |