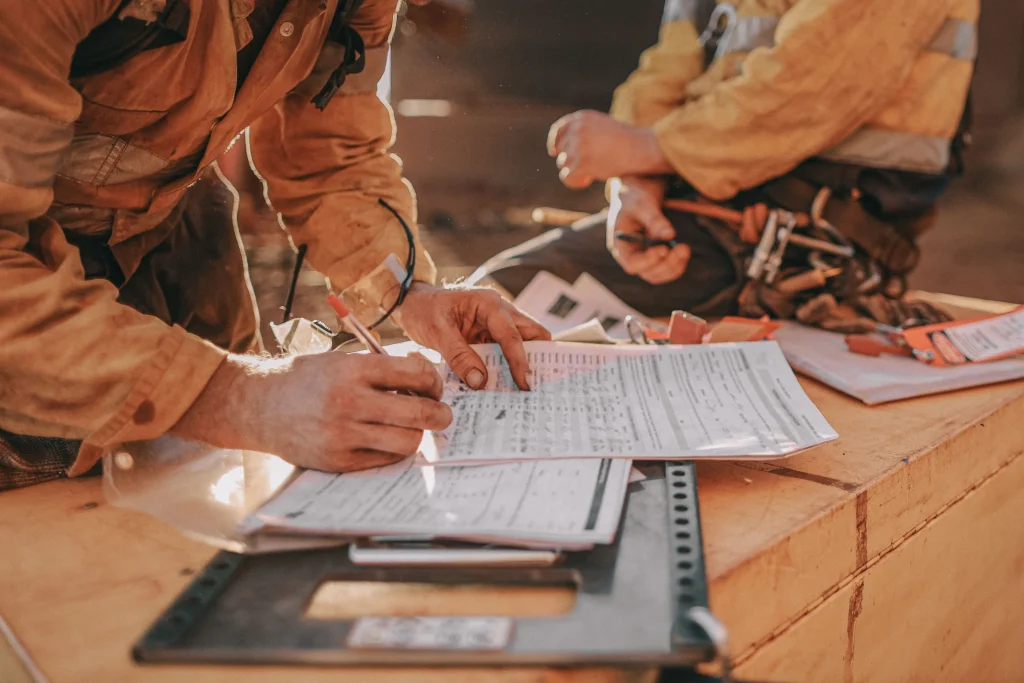
Manter as operações industriais funcionando de maneira contínua e eficiente é um desafio que requer atenção constante e planejamento meticuloso.
A manutenção regular é essencial para prevenir problemas e garantir a longevidade dos equipamentos e sistemas.
Por isso, paradas de manutenção bem planejadas podem evitar prejuízos significativos, garantir a produtividade e gerar mais lucros.
Neste blog, vamos falar sobre a importância dessas paradas e discutir os melhores métodos para realizar uma manutenção eficaz, minimizando impactos na produção.
A importância da manutenção
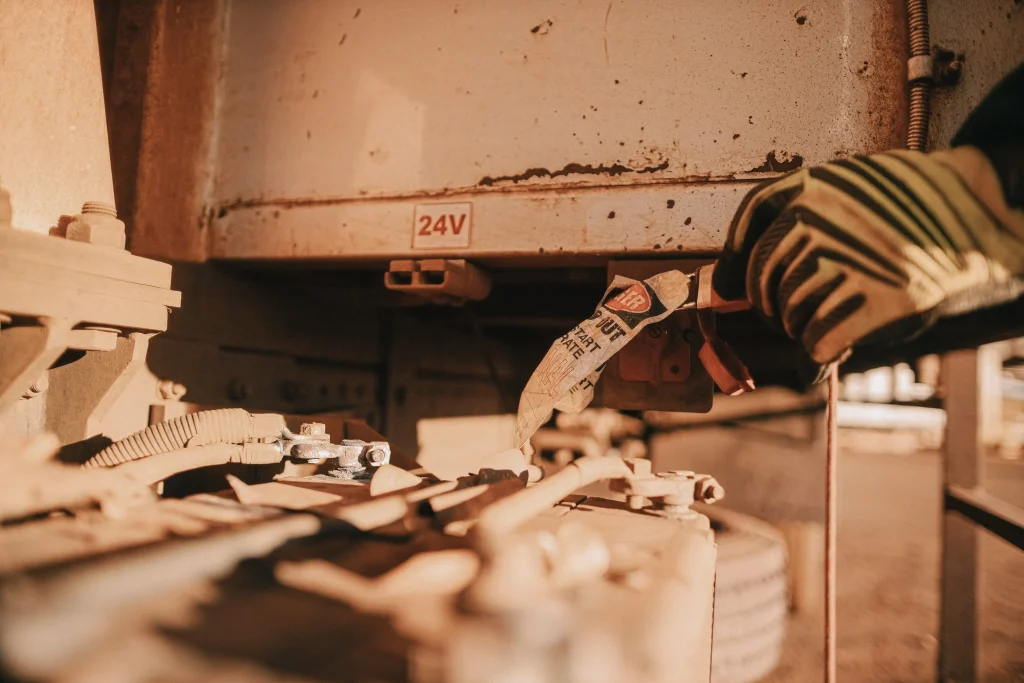
Manter os equipamentos operando de forma eficiente e segura requer cuidados nos detalhes.
Por isso, realizar atividades de manutenção regularmente, de forma organizada e planejada, é essencial para prevenir falhas e garantir o bom funcionamento dessas máquinas robustas.
Essa prática não apenas ajuda a evitar interrupções indesejadas na produção, mas também pode prolongar a vida útil dos equipamentos.
Então, a necessidade de substituições frequentes é reduzida, o que diminui os custos a longo prazo. Além disso, a manutenção adequada contribui para um ambiente de trabalho mais seguro e confiável.
Prejuízos de uma parada não programada
Paradas não programadas podem causar prejuízos elevados e complicações operacionais.
Quando um equipamento falha inesperadamente, toda a linha de produção pode ser impactada, resultando em atrasos, desperdício de materiais e aumento dos gastos.
Lembre-se: deixar de lucrar também é prejuízo.
Além dos custos diretos com reparos emergenciais, há também os custos indiretos, como a necessidade de pagar horas extras e a possível insatisfação dos clientes devido a atrasos.
Portanto, evitar essas paradas é fundamental para manter a produtividade e a competitividade da empresa.
Principais objetivos das paradas de manutenção
As paradas de manutenção são planejadas com objetivos claros e estratégicos para garantir a eficiência e segurança das operações industriais e, como já mencionado, evitar prejuízos por paradas não programadas.
Também, manter a integridade dos equipamentos é um dos grandes objetivos quando o assunto é parada de manutenção. Afinal, em um ambiente industrial, cada uma dessas máquinas pode custar milhares, senão milhões de reais.
Durante essas paradas, técnicos realizam inspeções detalhadas, identificam e corrigem problemas antes que se tornem críticos, e efetuam ajustes para melhorar a performance dos equipamentos.
Outro objetivo essencial é a melhoria da eficiência operacional. As paradas permitem a implementação de melhorias e atualizações nos sistemas, contribuindo para a otimização dos processos produtivos.
Operações contínuas
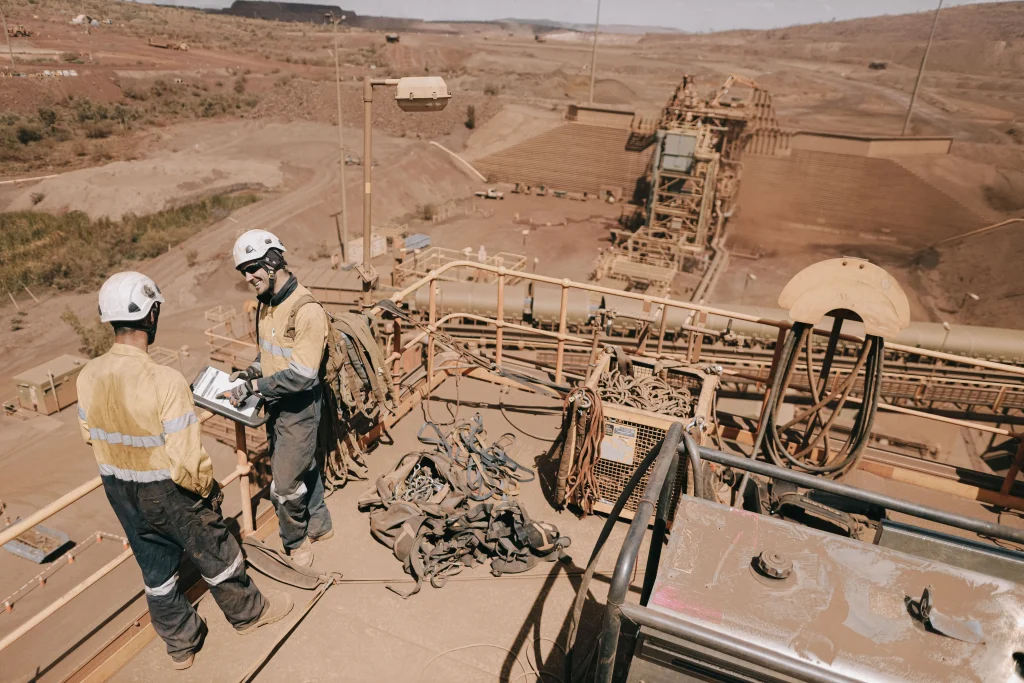
Em muitas indústrias, a necessidade de operações contínuas é uma realidade inevitável. Empresas que produzem bens de alto valor ou que operam em mercados altamente competitivos não têm tanta flexibilidade para interrupções na produção.
Setores como mineração, agronegócio e siderurgia muitas vezes operam 24 horas por dia, sete dias por semana. Nesses ambientes, qualquer parada pode resultar em perdas altíssimas, tanto financeiras quanto operacionais.
Portanto, a manutenção preventiva e preditiva é especialmente importante para garantir que a produção não seja interrompida.
Cenários de produção contínua e suas exigências
Operar de forma contínua exige um planejamento cuidadoso e uma infraestrutura eficiente.
Isso inclui sistemas de monitoramento em tempo real, equipes de manutenção prontas para agir rapidamente e estratégias de manutenção que possam ser executadas sem a necessidade de paradas prolongadas.
Empresas que operam dessa forma precisam de equipamentos confiáveis e de um plano de manutenção que permita intervenções rápidas e eficazes.
Além disso, a gestão eficaz das operações contínuas requer uma coordenação cuidadosa entre diferentes equipes e um planejamento detalhado para assegurar que todos os aspectos da produção sejam cobertos.
Correias transportadoras em setores diversos
As correias transportadoras também desempenham um papel fundamental em vários setores industriais que necessitam de garantias de operação constante, onde cada parada pode gerar uma perda de possibilidade de lucros.
Na mineração, essas correias são utilizadas para transportar grandes volumes de minérios, facilitando o fluxo contínuo de materiais e aumentando a produtividade.
A siderurgia depende das correias para mover matérias-primas e produtos acabados entre diferentes fases de produção, garantindo uma operação eficiente e integrada.
No agronegócio, as correias transportadoras são essenciais para o manuseio de grãos e outros produtos agrícolas. Elas otimizam processos como colheita, armazenamento e distribuição, reduzindo o tempo e os custos associados ao transporte de materiais.
Além disso, em usinas de energia e outros setores industriais que operam 24 horas por dia, as correias transportadoras garantem que o fluxo de materiais seja constante, minimizando interrupções e aumentando a eficiência.
Qual é o melhor momento para uma parada de manutenção?
Determinar o momento ideal para uma parada de manutenção, de forma organizada, é fundamental.
Essas programações devem ser cuidadosamente planejadas para coincidir com períodos de menor demanda ou durante intervalos já previstos no cronograma de produção.
Por exemplo, no setor agrícola, realizar manutenções durante a safra pode ser extremamente arriscado, pois esse é um período de alta demanda e qualquer interrupção pode resultar em grandes perdas financeiras.
Portanto, o ideal é programar essas paradas para os períodos de entressafra, quando a atividade é menor e a manutenção pode ser realizada sem prejudicar a produção.
Isso permite que os reparos sejam feitos com o menor impacto possível na operação.
Dificuldades nas paradas de produção para manutenção
Realizar paradas de produção para manutenção apresenta vários desafios, especialmente em indústrias que operam de forma contínua.
As dificuldades incluem a necessidade de coordenar diferentes equipes e fornecedores, a complexidade de gerenciar um grande número de tarefas simultaneamente e o risco de atrasos que podem prolongar a interrupção.
Além disso, qualquer falha na execução do plano pode resultar em aumentos de custos e tempos de parada maiores do que o previsto.
Tipos de manutenção
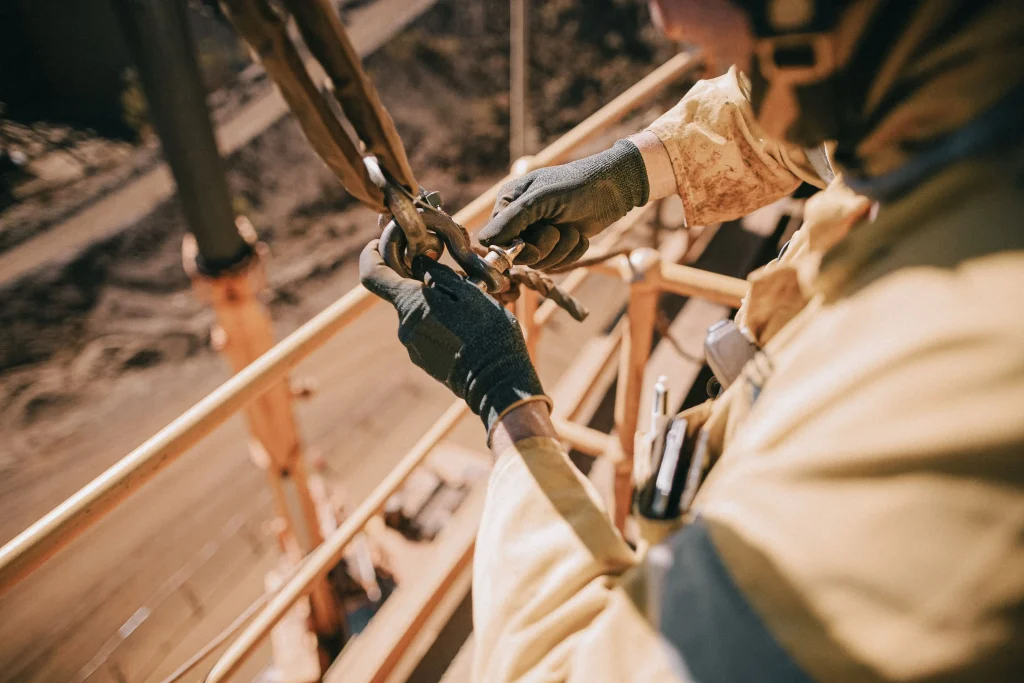
Existem vários tipos de manutenção, cada um com características e objetivos específicos para garantir a eficiência e a longevidade dos equipamentos. Os principais tipos de manutenção são a preventiva, preditiva e corretiva.
Manutenção preventiva
A manutenção preventiva é realizada em intervalos regulares, com o objetivo de reduzir a probabilidade de falhas e manter o desempenho dos equipamentos.
Essa prática inclui atividades como lubrificação, calibração e inspeções gerais, baseadas em um cronograma previamente definido.
Manutenção preditiva
A manutenção preditiva utiliza tecnologias avançadas para monitorar continuamente os equipamentos, identificando possíveis problemas antes que se tornem críticos.
Sensores de vibração, temperatura, pressão e outros parâmetros são usados para detectar sinais de desgaste ou mau funcionamento.
Isso permite que as intervenções sejam planejadas de acordo com a condição real dos equipamentos, evitando desmontagens desnecessárias e reduzindo custos.
Manutenção Corretiva
A manutenção corretiva é realizada após a ocorrência de uma falha. Esse tipo de manutenção pode ser planejado ou não planejado.
A manutenção corretiva planejada ocorre quando a falha é detectada durante atividades de monitoramento e pode ser agendada para minimizar o impacto na produção.
Já a manutenção corretiva não planejada acontece de forma emergencial, quando um equipamento quebra inesperadamente, resultando em paradas abruptas e potenciais prejuízos.
Embora seja a forma mais reativa de manutenção, ela ainda é necessária para corrigir problemas que não puderam ser previstos ou evitados por outros tipos de manutenção.
Como planejar uma parada de manutenção?
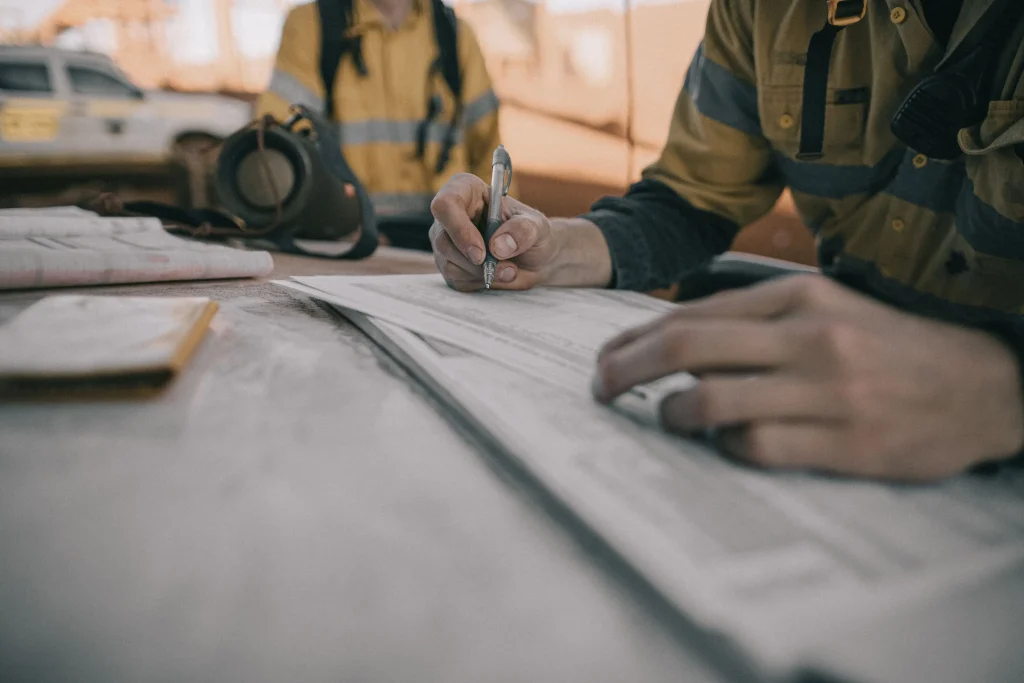
Planejar uma parada de manutenção é um processo que exige organização e coordenação para minimizar o impacto na produção e garantir a eficiência das operações.
Aqui estão algumas etapas e considerações importantes para um planejamento eficaz:
1. Avaliação geral dos equipamentos
Realizar avaliações completas dos equipamentos para identificar necessidades específicas de manutenção. Coletar dados sobre desempenho, histórico de falhas e condições atuais.
2. Planejamento detalhado
Elaborar um plano que inclua todas as atividades de manutenção necessárias, definindo objetivos, tarefas, recursos e um cronograma realista. Isso ajuda a organizar e priorizar as ações de manutenção.
3. Coordenação das equipes
Garantir uma comunicação eficaz entre todas as equipes envolvidas. Realizar reuniões para alinhar expectativas, definir responsabilidades e garantir que todos estejam cientes do cronograma e das atividades.
4. Utilização de tecnologias
Utilizar tecnologias de monitoramento e controle, como sensores e softwares de gestão, para otimizar o processo de manutenção. Isso permite prever falhas e planejar intervenções de forma mais eficiente.
5. Execução e monitoramento
Acompanhar a execução das atividades conforme o plano estabelecido, resolvendo problemas e fazendo ajustes conforme necessário para garantir que o cronograma seja cumprido.
6. Documentação e análise
Documentar todas as atividades realizadas e analisar os resultados para identificar áreas de melhoria. Isso ajuda a melhorar o planejamento de futuras manutenções e garante a eficiência operacional a longo prazo.
Monitoramento 24/7 para evitar paradas não programadas
Sistemas de monitoramento com inteligência artificial são cruciais para detectar variações anormais nos parâmetros operacionais, como temperatura, vibração e pressão.
Essas tecnologias permitem uma análise contínua e detalhada do desempenho dos equipamentos, prevenindo falhas e aumentando a confiabilidade das operações.
Sistemas de monitoramento Mercúrio
HX170
O sistema de monitoramento HX170 da Mercúrio é projetado para garantir a supervisão contínua das correias transportadoras. Ele utiliza sensores avançados para medir e analisar diversas variáveis em tempo real, como a tensão e o desgaste da correia.
Com esses dados, é possível prever falhas e realizar manutenções preventivas de maneira eficiente, evitando paradas não programadas que podem causar prejuízos significativos.
HX270
O HX270 é outro sistema de monitoramento da Mercúrio, focado na análise detalhada e precisa do desempenho das correias transportadoras.
Ele incorpora tecnologias de ponta, como sensores de alta precisão e software de análise preditiva, que ajudam a identificar problemas potenciais antes que eles se tornem críticos.
Esse sistema é essencial para garantir a continuidade das operações e a segurança dos equipamentos, minimizando o risco de falhas inesperadas.
Correias Mercúrio: garantimos o funcionamento seguro da sua operação
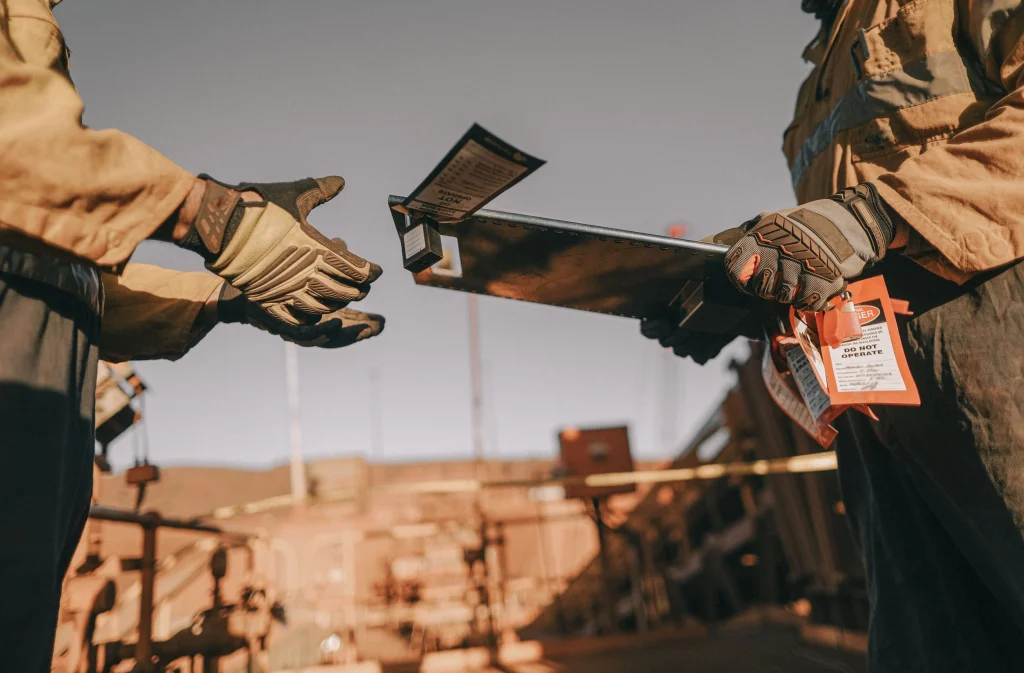
Na Mercúrio, entendemos a importância de garantir o funcionamento contínuo e seguro das operações industriais.
Nossas correias transportadoras são projetadas para suportar as condições mais exigentes, oferecendo durabilidade e eficiência em diversos setores, como mineração, siderurgia e agronegócio.
Utilizamos tecnologias avançadas em nossos sistemas de monitoramento, como o HX170 e o HX270, para proporcionar uma supervisão contínua e detalhada do desempenho das correias.
Esses sistemas são essenciais para identificar problemas em seus estágios iniciais e permitir a tomada de ações preventivas. Isso não só minimiza o risco de paradas inesperadas, mas também prolonga a vida útil dos equipamentos e aumenta a produtividade.
Por aqui, estamos comprometidos com a excelência e a inovação para oferecer as melhores soluções em correias transportadoras e sistemas de monitoramento que evitam prejuízos e garantem segurança operacional.